CREATION DE VALEURS
EXPERT EN ORGANISATION INDUSTRIELLE
C’est le cœur de l’entreprise industrielle, où se crée la valeur qu’achète le client. A la croisée de la supply chain et du cycle de vie produit.
CREATION DE VALEURS
ORGANISATION INDUSTRIELLE
Derrière cette notion « d’organisation industrielle » se cache de nombreux concepts. Le premier qui vient à l’esprit est celui de la performance celui qui préoccupe en premier lieu chaque dirigeant. Elle est nécessaire à plusieurs titres mais largement insuffisante.
Il y a pour nous plusieurs notions incontournables à maitriser dans l’organisation industrielle et de nombreux outils peuvent y contribuer en intégrant une vision d’ensemble.
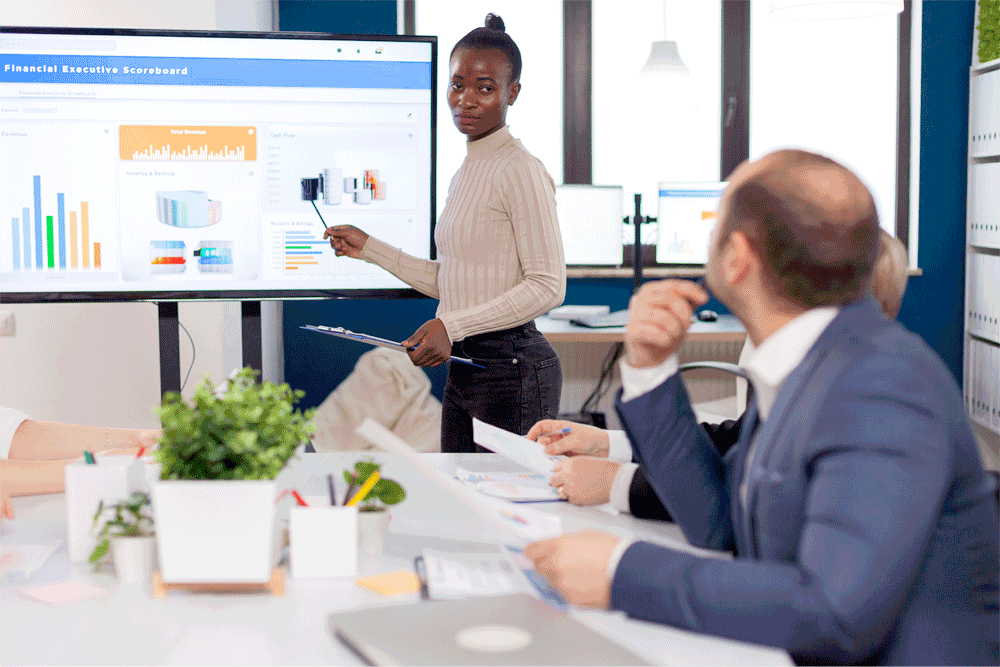
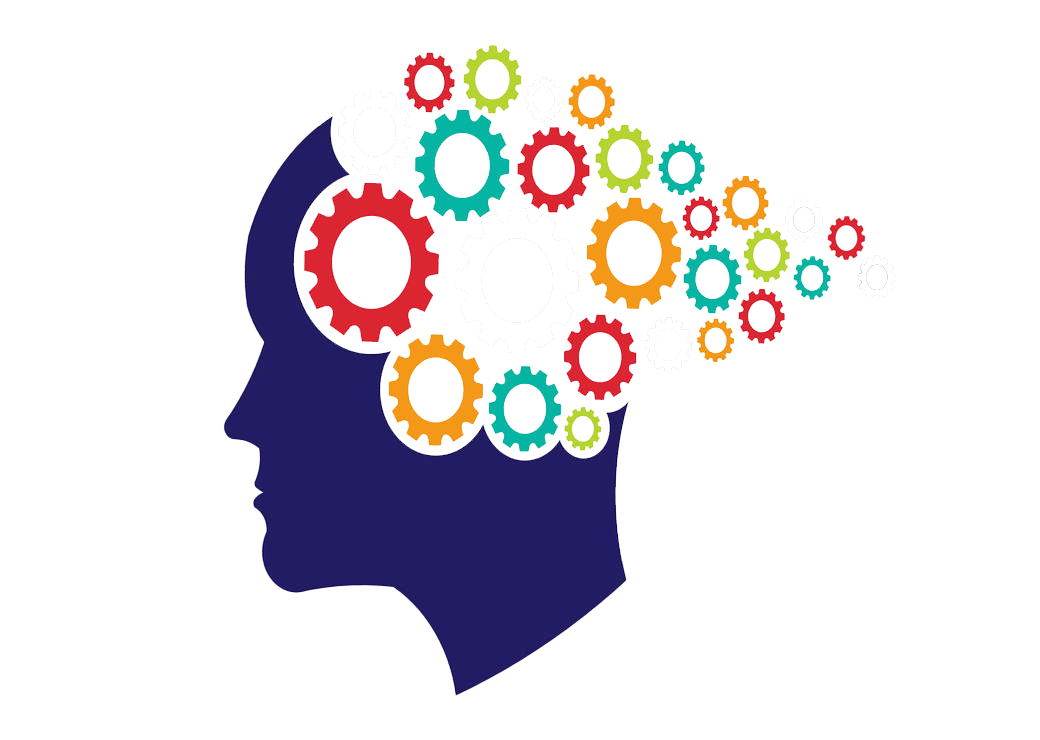
Stabilisateur
L’AMÉLIORATION CONTINUE : UN CYCLE VERTUEUX
On peut penser qu’il s’agit d’une idée à contre-courant dans notre monde VUCA où tout va vite, très vite. L’amélioration continue s’inscrit dans un temps long. C’est pourtant un changement culturel indispensable. C’est d’abord un changement d’esprit qui vise à rendre actif l’ensemble des acteurs, et sortir du découpage vertical taylorien.
Le chemin n’est certes pas aisé, mais la mise en place de l’amélioration continue est un stabilisateur systémique indispensable à l’atteinte des objectifs de l’entreprise.
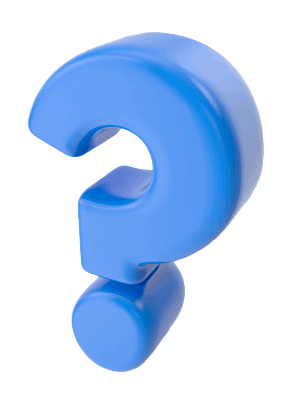
Qui dans votre entreprise est force de proposition et acteur des évolutions aussi minimeS soient-elles ?
Le premier gain de la mise en place d’une politique d’amélioration continue c’est le développement des compétences des parties prenantes. Trouver des solutions qui amènent des améliorations à la chaine de production de valeur. Mais plus important : c’est mettre les parties prenantes en mouvement.
Le deuxième gain de l’amélioration continue c’est de pouvoir prendre le relais à des projets (et parfois de les initier). Un peu comme le caillou que vous lancez dans la marre, chaque transformation que vous faites dans votre entreprise provoque une perturbation proportionnelle aux transformations engendrées. Au bout d’un certain temps votre marre reprend son aspect de miroir. C’est comme si vous n’aviez rien fait et cela se passe souvent de la même manière dans l’entreprise. « Retour à la case départ ! ». L’amélioration continue par son mouvement permanent permet de consolider les gains des projets de transformation réalisés et d’éviter le retour à la case départ.
Le troisième gain que vous devez percevoir derrière ce processus que les Japonais nomment KAIZEN c’est un gain de connaissances. Des connaissances à la fois techniques et humaines.
Des RESSOURCES RARES
Réduire les gaspillages.
Cela commence dès la conception et ne s’applique pas seulement à la production. Si l’on se place du côté du client, ce dernier a des besoins équivalant à une valeur ajoutée nécessitant une quantité d’énergie et de moyens (N). Et pour répondre à ces besoins vous allez utiliser une quantité d’énergie, de moyens (M).
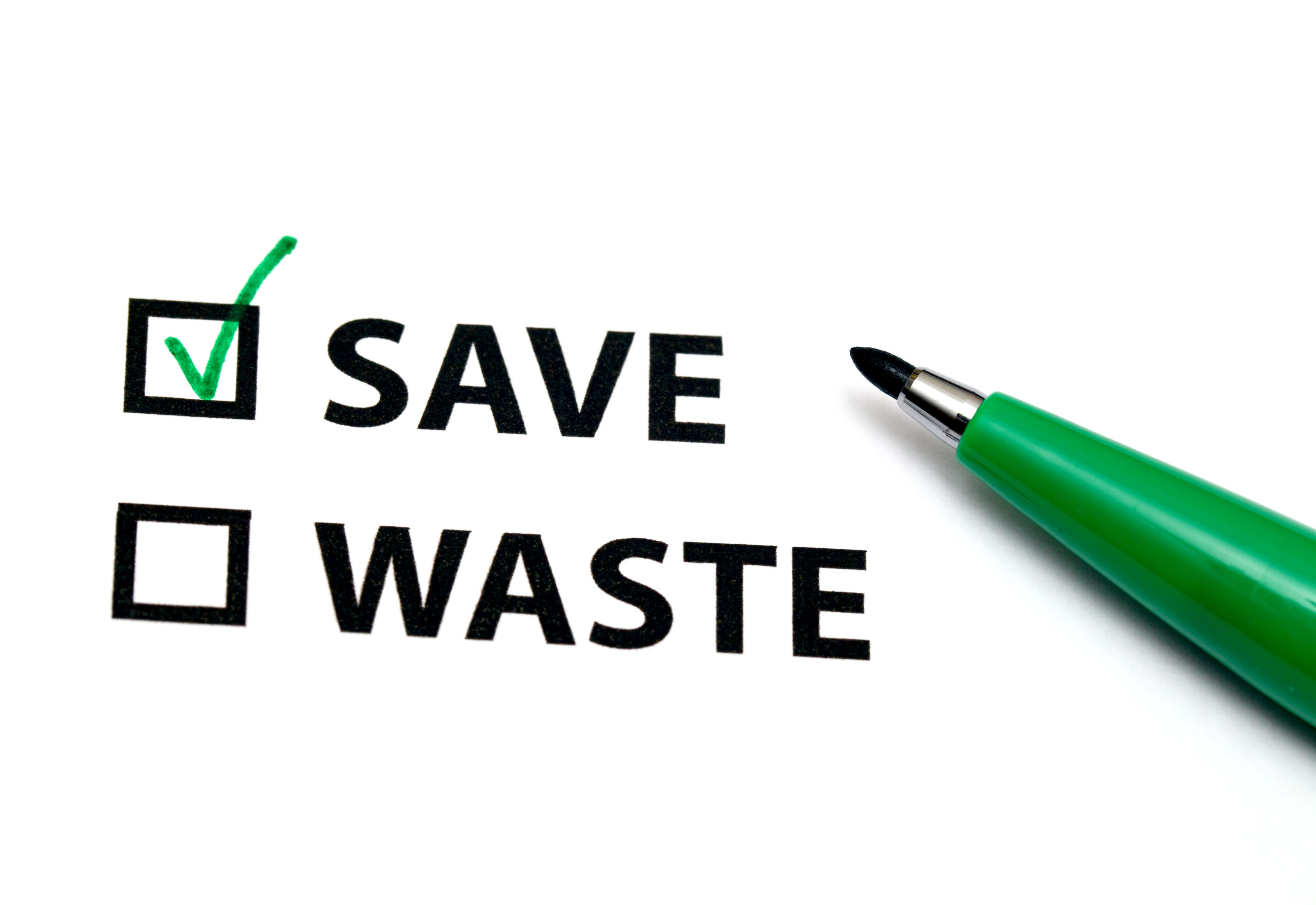
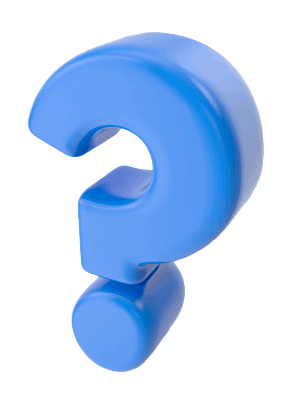
Dans l’idéal N/M tend vers 1. Vers quoi tend ce rapport N/M dans votre entreprise ?
1
0,5
0,1
0,01
En avez-vous une idée ?
Le Lean qui en anglais signifie maigre a donné son nom au modèle Toyota dans sa réappropriation américaine dans les années 1990. Les gains sont importants et incontournable dans une concurrence mondiale. Cette méthode s’appuie sur la recherche des Gaspillages (MUDA en japonais). On en compte de 7 à 10 selon la littérature.
Un premier gain qui vient à l’esprit ici est la suppression de certaines dépenses liées à l’utilisation des ressources (Matérielles et humaines). Les gaspillages de matière première c’est bon à la fois pour le porte-monnaie mais aussi pour la planète. Pour l’activité humaine, cela permet soit de produire autre chose soit de l’orienter sur l’amélioration continue et d’enrichir l’entreprise de connaissances et d’autres gains.
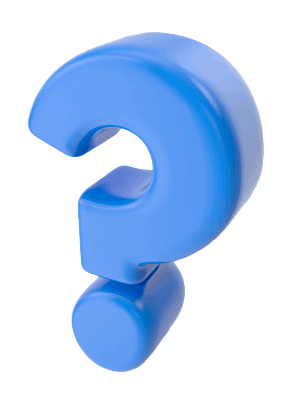
Et vous où en êtes-vous ? Quelle est la surface occupée par vos stocks ?
5%
15%
40%
80% ?
Un deuxième gain est directement financier en réduisant les immobilisations dans les stocks. Les niveaux de stock sont révélateurs de la maturité de l’entreprise. Un bon fonctionnement avec un niveau de stock faible révèle une bonne maîtrise du processus industriel. Et on l’observe à travers des surfaces et des volumes occupés.
Un troisième gain à travers la réduction des délais. C’est aujourd’hui un enjeu critique. Cela peut devenir un avantage concurrentiel, autant sur le cycle de développement produit, que dans le pipeline de la chaine d’approvisionnement (Supply Chain).
Connaissez-vous la tension de flux de vos cycles de développement ou ce de votre chaine d’approvisionnement ?
Quelles sont les attentes de votre marché, que font vos concurrents ?
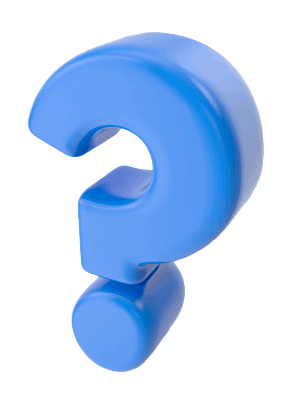
AGILE MAIS PAS VERSATILE
S’adapter à l’environnement
L’agilité est une nécessité dans un monde « VUCA ». Tirer des méthodes agiles (Manifesto Agile de 2001) est un état d’esprit. Il existe aussi quelques méthodes intéressantes à intégrer dans les organisations comme le SCRUM ou le KANBAN. Ces méthodes sont issues d’une analyse de l’approche LEAN sortie du contexte de production industrielle.
Au-delà du discours êtes-vous agiles ? Quel est votre capacité d’adaptation ?
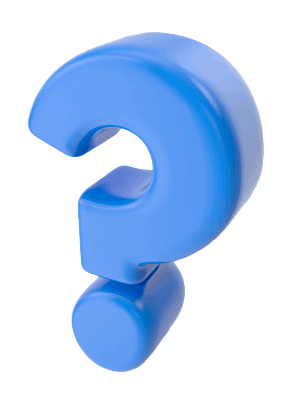
Un premier gain dans la relation et l’orientation client. Le suivi de la satisfaction client permet de le fidéliser. Il faut faire preuve, il est vrai, d’une certaine assurance et d’un état d’esprit plutôt transparent. Ce feedback client régulier assure une meilleure utilisation des ressources et évite le gaspillage de temps des acteurs du projets.
Un deuxième gain dans cette conduite se trouve dans le pilotage à horizon court de l’action. Cela permet d’agir au bon moment avec les bonnes informations. Cela évite de refaire différentes actions (Planning, études…) avec les effets sur la motivation des acteurs. Ce pilotage permet aussi de gérer les goulots d’étranglement, les points durs rencontrés par les acteurs.
Un troisième gain dans l’acquisition de compétences à travers les feedbacks réguliers et le processus d’amélioration continue de l’organisation. On amplifie les gains de l’amélioration continue.
DE L’URGENCE À L’ESSENTIEL
Sortir du mode pompier.
Au volant de votre voiture, ou sur un marathon, c’est avant tout la régularité qui compte. Si vous conduisez avec une forte alternance d’accélérations et de freinages, vous allez consommer beaucoup de carburant. Si vous vous alternez course rapide et arrêt sur une course longue, vous risquez de ne pas voir la ligne d’arrivée. La régularité est une source d’optimisation des consommations d’énergie mais s’il est parfois nécessaire de passer outre. D’un point de vue industriel la méthode six sigma développée par Motorola dans les années 1980 permet de stabiliser les processus. Elle identifie les biais (Dérive par rapport à la cible) et aussi les bruits et autres interférences dans le processus.
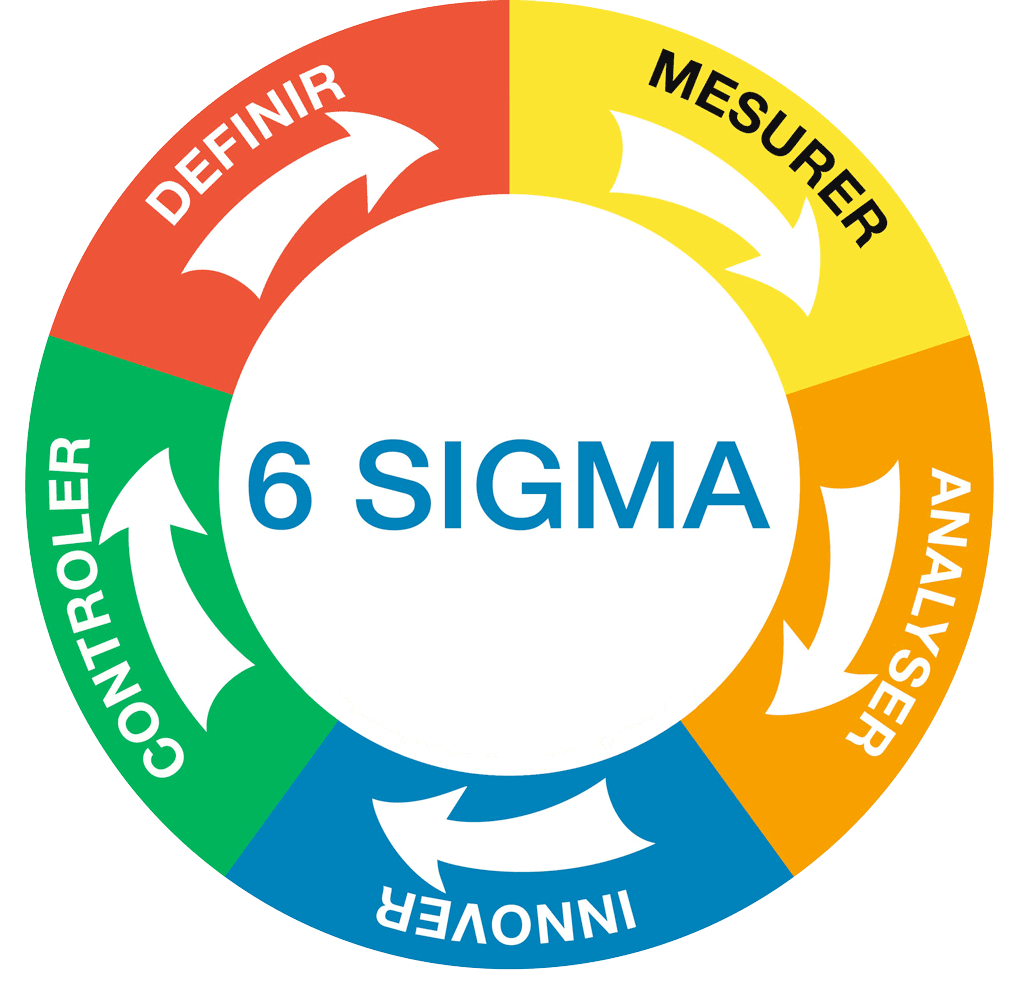
Où en sont vos processus ? QuelLEs sont leurs capabilités ?
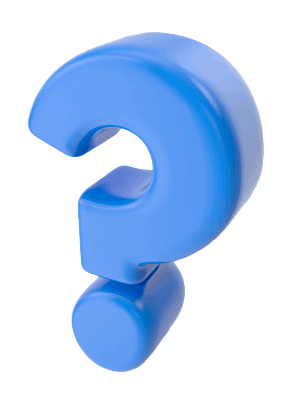
Un premier gain avec la régularité dans la maitrise du processus et des délais et ses conséquences :
· La satisfaction d’un client livré dans les temps
· La réduction du mode pompier et des coûts associés
· La réduction des stress générés par le mode pompier
Un deuxième gain avec un niveau de qualité supérieure et donc la satisfaction client sans passer par du contrôle, de la réparation….
Un troisième gain avec la connaissance réutilisable pour d’autres développements ou d’autres productions.
Quand et comment nous vous apportons le plus de valeur ?
En organisation industrielle l’approche proposée trouve son efficience à trois étapes importantes
Dans la mise en lumière des contradictions
Dans la cartographie des parties prenantes et la visualisation de votre écosystème
Dans la clarification des besoins des parties prenantes
Dans un cas comme dans l’autre vous y gagnerez en temps, en efficience et en sérénité vis à vis de l’ensemble de vos parties prenantes